Lost wax casting is a great technique for making original and interesting jewelry components. Lots of jewelers use it to produce their own designs. The best part is you can use your original model to subcontract some of the work for your jewelry by having a caster cast and polish your pieces for you.
The process is simple. In a nutshell, you create a wax model of your design. That wax model is set inside a steel flask and covered with plaster investment, leaving a funnel and tunnel to reach the wax through the hardened plaster. The flask is put into a kiln and the wax is "lost" as it's burned out of the flask. The flask is placed in a casting machine and the void left behind in the plaster is filled with molten metal. To see the process from spruing the wax through casting, watch this little video I've made. You may need the QuickTime plugin for Mac or PC to view the video.
5 Reasons to Cast your own Designs
1) Design your own original clasps, charms and jewelry to match your style and vision. If you are creative enough to make jewelry, you've probably already had dozens of ideas for parts you wish you could buy. Make them for yourself. Stand apart from other jewelers.
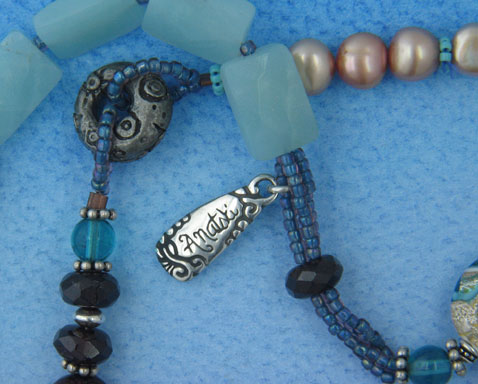
2) Add name recognition to your jewelry with a beautiful custom tag with your name or logo. Let them know when they have one of your original designs and make it clear and beautiful.
3) Design your own line of jewelry with a few unique pieces. It doesn't take a lot to get started, maybe as few as a half a dozen models. If you design them to mix well, you can create lots of variations and a distinctive line of your own original jewelry.
4) Stop using the same findings as other designers! Do you know how many jewelers are out there competing for the same customers? Half of most vendors at craft shows are jewelers. Stand apart right away from most of the pack with your own original designs, unique to you and your line.
5) Cast the same design in the metal of your choice: sterling, bronze, gold. You can stretch your investment, and lower costs by casting in a variety of metals, from the same wax model and the same mold.
Leverage your time and save money with Lost Wax
Leverage your time and save money with Lost Wax
Every designer struggles with how to define their work, how to express themselves through their creations. The lost wax technique gives you a whole different level of freedom for bringing your ideas to life. In wax, you can sculpt and build up forms that would be almost impossible by regular soldering and fabrication techniques. The tools you need to make wax models are simple and home friendly. You can outsource the labor intensive casting, molding and reproduction to another company that can do the work for you in a fraction of the time.
And if you're selling your jewelry, this technique can leverage your time. While you're working on shows, new designs, and all the rest you have to do to make it as a jeweler, your pieces are being cast and polished by professionals. All you have to do is tag it or assemble it into great jewelry. Plus, by subcontracting the casting, you can fix the price of labor and materials for your pieces, which helps you with your bottom line.
What can you make with Lost Wax Casting?
![]() |
![]() |
![]() |
The only limit is your imagination. A lot of what you see in catalogs and stores has been cast. Casting your parts not only adds originality and value to your jewelry, it can save you time. If you fabricate some of your parts for your jewelry, you could save time by having them cast for you instead.
Learn Lost Wax Casting and Wax Carving
Learn all you need to know to get started with this great technique at the Silvera Jewelry School, in Berkeley, CA.
The first class, Lost Wax Casting, teaches you about the casting process, about outsourcing your casting to casters, and most importantly, introduces you to the basic techniques for making your own wax models - carving, build up, polishing, etc. Students will even learn how to polish their finished casting during the workshop.
Continue learning more about wax work with our follow up workshops, like Figurative Wax Carving, and Lost Wax Stone Setting.
![]() |
Figurative Wax Carving |
![]() |
Lost Wax Stone Setting |
Post your questions about lost wax casting here, if you like. I'd be happy to help.